新規立上げ品での測定器準備PDFダウンロード
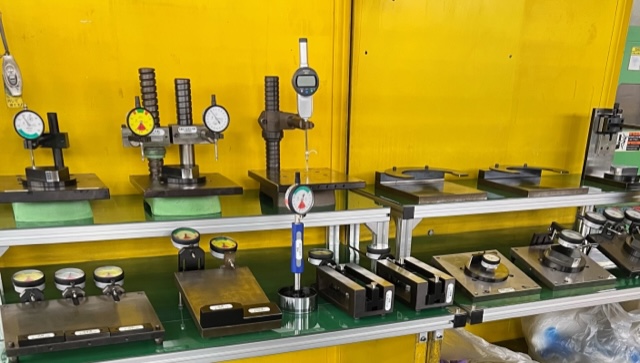
新規製品の受注から生産開始まで
顧客から新規製品を受注した際、受注決定から実際の納入までに、下記に示したことを実施していくことになります。この場合の新規製品とは、毎月継続して受注のある”量産品”のことで”号口品”とも呼びます。
- 加工・組立するための生産設備の整備
- 測定器・検査具などの整備
- 品質計画書を構成する標準・帳票類の作成
- 生産を担当するオペレータの教育
- 試作品の製作と納入
これらの製品実現のための準備プロセスを「生産準備プロセス」と呼びます。
さて、「生産準備プロセス」がほぼ完了した時点で、製品の量産を開始するにあたり「生産準備プロセス」の全項目の完了を確認します。これを「工程整備完了確認」をと呼びます。「工程整備完了確認」では、生産工程でのハードおよびソフトの整備状況が充分であること、造られる製品の品質が顧客図面規格を満足していること、設備が充分な工程能力をもっていることなど確認します。
測定器・検査具などの整備
1)工程毎の検査内容の決定
受注した製品の顧客図面を元に、加工工程や順、そして、それぞれの工程で実施する加工内容および検査内容を決定します。それをまとめたものが、下表の「QC工程表」「検査規格」と呼ばれる標準類です。
標準類名称 | 内容 | 含まれる項目 |
QC工程表 | [品番単位で作成] 材料・部品から完成品として出荷されるまでの工程順に、各工程で実施する品質管理特性や管理内容を示す | 工程フロー、工程名、設備名、検査内容・規格・頻度・方法 |
検査規格 検査基準書 | [品番単位で作成] 製造工程での製品検査内容を示す | 検査内容・規格・頻度・方法 等 |
2)測定器の選定
「QC工程表」および「検査規格」を作成するにあたり、製品品質を保証するための検査内容に対し最適な測定器を選定します。その際、測定器は下記項目のような観点に立って検討し、選定されます。
- 使用目的、測定対象、測定項目、必要精度および要求される計測能力に適する測定器を選定する。特に、人的要因による測定誤差をできる限り小さくするための測定器を選定する。
- 工程能力や管理図などによるプロセス管理および工程内における寸法補正の必要性のため、数値測定を基本とする。
- 数値測定が困難な場合や測定の効率向上およびヒューマンエラー防止の必要がある場合は、限界ゲージの使用を検討する。
なお測定器の選定における留意点については、下記記事(「測定器の選定」)においても説明していますので参照ください。
3)測定器の設計
使用する測定器を決定したらその設計を行います。既にあるものであればそのまま利用し、新たに検討する必要があれば、図面を起こします。
4)測定器の調達(手配・発注)
設計した測定器の図面に元に、部品を手配します(自作、社外に発注など)。合わせて、必要なマスターリング、マスターブロック、ダイヤルゲージ、測定台・検査台などを発注します。
測定器の部品やダイヤルゲージなどが揃ったら測定器を組立て、完成させます。
5)ラインへの測定器の整備
すべての測定器やマスター、検査台・測定台などが揃ったら対象製品のライン・サイドに設置します。
その際、測定効率および品質向上の面から検査者がラインで加工された対象ワークを持ち運ぶ距離を極力短くなるように検査台・測定台を設置します。ここで品質向上の面というのは、類似製品などを隣のラインで加工しているケースで異品混入やチョイ置き(本来置かれるべきでない場所にワークを仮置きすること)を防止するなどです。
設置した検査台・測定台に測定器やマスターを測定項目にあわせて測定し易い順番で並べます(冒頭の写真参照)。
* kensatoolsがお手伝いできること!!
上記のステップの中で、2)測定器の選定、3)測定器の設計、4)測定器の調達(手配・発注)にはかなりの時間が必要です。品質管理を担当者にとって、定常業務をこなしながらこれらのプラスの作業を行うことは時時間的な余裕がなく、困難ですので予め余裕をもったスケジューリングが求められます(加工業の当社もそうなのでよく理解できます)。
そんな時には、kensatoolsがお手伝い致します。まずは相談してください。